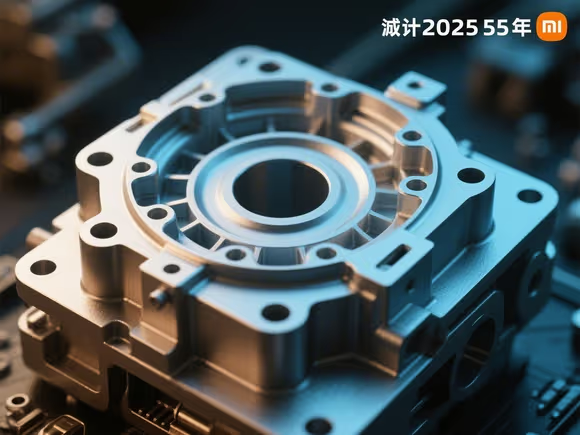
根据 2025 年最新信息,小米在一体化压铸技术的应用上已进入深化阶段,不仅实现了技术参数的领先,还将其扩展至更多车型和关键部件。以下是具体进展:
一、技术应用与创新
- 核心技术突破
小米自研的9100 吨一体化压铸机(比特斯拉的 9000 吨机型更大)已在 SU7 系列车型中量产应用,结合自主研发的泰坦合金材料,将原本 72 个零部件整合为单一压铸件,焊点减少 840 处,车身减重 17%,同时提升防撞能力和 NVH 性能。这种技术突破不仅降低了生产成本,还使车身扭转刚度达到 43000N・m/deg,显著提升车辆整体稳定性。
- 材料与工艺协同
通过 AI 仿真系统从万种合金配方中筛选出的泰坦合金,具备高强度和抗疲劳特性,尤其适用于一体化压铸工艺。例如,SU7 Ultra 的车身结构件采用该材料后,焊接点减少带来的结构完整性优化,使其在碰撞测试中表现优于传统焊接工艺车型。
二、车型扩展与产能布局
- 新车型全面覆盖
除已上市的 SU7 系列外,小米计划于 2025 年底发布的中大型纯电 SUV “昆仑”(内部代号)也将采用一体化压铸车身,续航超 700 公里,并配备激光雷达支持城市 NOA 功能。这表明小米正将该技术从轿车扩展至 SUV 领域,形成全车型技术覆盖。
- 产能提升与供应链保障
小米北京工厂目前年产能为 30 万辆,通过引入 T9100 压铸工艺和双班制生产,单月交付量已突破 2 万台。二期工厂预计 2025 年中投产,新增 15 万辆产能,主要用于生产新车型 YU7,进一步缓解订单压力。供应链方面,文灿股份、博俊科技等企业为小米提供高精度模具和压铸件,良品率超 95%,确保技术落地的稳定性。
三、行业影响与未来趋势
- 技术引领行业变革
小米的一体化压铸技术已成为行业标杆,其 9100 吨压铸机的量产应用推动了国内压铸设备向万吨级发展。车百智库研报指出,该技术使生产效率提升 79 倍,车型开发周期缩短 1/3,且材料利用率从传统工艺的 50%-60% 提升至 95%。这种效率优势正促使更多车企加速布局类似技术。
- 智能化与制造协同
小米将一体化压铸与智能制造深度融合,例如通过数字孪生技术优化生产流程,将整车生产节拍压缩至 68 秒 / 台,零部件通用化率达 78%。此外,AI 技术在材料研发(如电解液配方筛选)和实验自动化(如深云智合的智能实验室)中的应用,进一步缩短了技术迭代周期。
四、用户价值与市场反馈
- 性能与体验提升
一体化压铸带来的轻量化(SU7 四驱版车重仅 1980kg)和结构优化,直接提升了续航表现(SU7 Max CLTC 续航突破 900 公里)和驾驶质感。同时,焊点减少降低了车身异响概率,配合全域智能热泵系统,冬季续航达成率提升至 83%。
- 市场认可与订单压力
截至 2025 年 3 月,小米 SU7 标准版订单交付周期已延长至 35-38 周,部分配置甚至需等待至年底提车。这反映出市场对其技术的高度认可,但也凸显了产能扩张的紧迫性。二期工厂投产后,小米计划 2025 年实现 30 万辆交付目标,以缓解供需矛盾。
五、挑战与应对
- 技术复杂性与成本控制
尽管一体化压铸大幅降低了生产环节成本,但其前期设备投资(如压铸机、模具)较高。小米通过自研设备和与宁德时代等企业的联合研发,有效分摊了研发成本,并通过规模化生产逐步摊薄边际成本。
- 供应链韧性建设
为保障泰坦合金等关键材料的稳定供应,小米已投资瑞隆科技(电池回收)、云山动力(大圆柱电池)等企业,形成 “材料 - 制造 - 回收” 闭环。同时,与钢研集团等机构合作开发高性能材料,确保技术领先性。
综上,2025 年小米的一体化压铸技术已从单一车型应用升级为全产品线战略,其自研设备、材料创新与智能制造的协同,不仅巩固了市场竞争力,也为行业树立了技术标杆。随着产能扩张和新车型推出,这一技术有望进一步推动新能源汽车制造效率的提升。
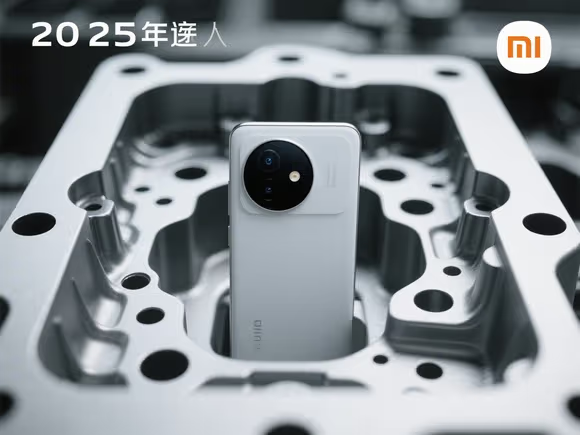