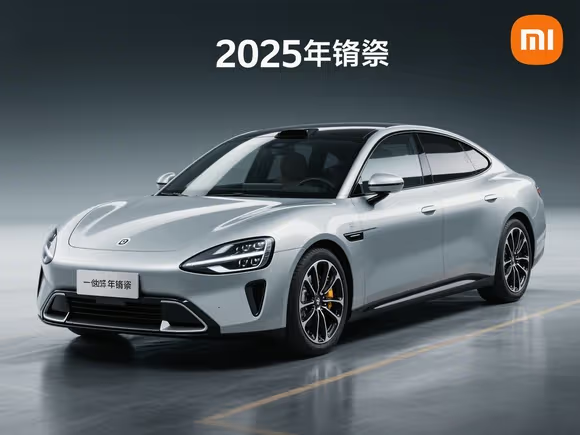
根据目前的信息,2025 年小米汽车的车身确实采用了一体化压铸技术。以下是关键细节和技术突破的分析:
一、核心车型的技术应用
小米 SU7 系列(包括标准版、Pro 版和 Max 版)均明确采用一体化压铸车身。例如,程力汽车集团官网的解析指出,SU7 通过一体化压铸技术实现了卓越的结构强度和稳定性。而 2025 款 SU7 Ultra 的车身扭转刚度达到 43000N・m/deg,同时车重控制在 1980kg(四驱版),这一轻量化与高强度的平衡正是一体化压铸工艺的典型优势。此外,新曝光的中大型纯电 SUV「昆仑」(内部代号)也将延续这一技术,进一步扩大应用范围。
二、生产工艺与设备突破
小米自建的北京亦庄工厂配备了自研的9100 吨压铸岛集群,这一设备规模比特斯拉上海工厂的 6000 吨设备大 50%,甚至超过其美国工厂的 9000 吨设备 100 吨。该压铸岛由 60 台设备组成,通过 433 项工艺参数的精准控制,实现每 76 秒下线一台车的生产效率,且车间关键工艺(如压铸、冲压)实现 100% 自动化。这种全栈自研能力使小米成为国内唯一同时拥有量产压铸合金材料(小米泰坦合金)和自研压铸设备集群的车企。
三、材料与结构创新
小米在一体化压铸中采用了纳米晶合金材料,这种材料不仅提升了车身强度,还通过「三明治」夹层地板设计增加了座舱垂直空间 50mm。同时,车身结构中高强度钢和铝的比例超过 90%,最高强度达 2000MPa,配合钢铝混合设计,在保障安全性的同时优化了续航表现。例如,SU7 的电池包通过 CTB 倒置电芯技术,碰撞安全性能提升 48%,车内空间增加 5%。
四、行业影响与技术争议
尽管一体化压铸技术存在初期设备成本高(单台压铸机超 6000 万元)、良品率波动(行业普遍 80%-95%)等挑战,但小米通过供应链整合(如文灿股份的 9000T 压铸机量产中底板,良品率突破 95%)和工艺优化,将该技术转化为竞争力。此外,小米的压铸岛集群通过 AI 主动优化压射参数设定系统等 11 项专利创新,解决了传统工艺的局限性。
五、未来技术延伸
2025 年小米的技术布局不仅限于现有车型。例如,SU7 Ultra 的赛道版电池包采用高功率设计,配合电机立体油冷系统,实现纽北连续两圈高速行驶不过热。而计划 2027 年量产的固态电池(能量密度 400Wh/kg)和 5 分钟快充技术(充电 5 分钟续航 200 公里),将进一步巩固其在电动化领域的领先地位。
综上,小米汽车在 2025 年已将一体化压铸技术从 SU7 系列扩展至新车型,并通过设备自研、材料创新和供应链协同,构建了从生产到性能的完整技术闭环。这一工艺的应用不仅提升了产品竞争力,也为行业树立了智能化制造的新标杆。
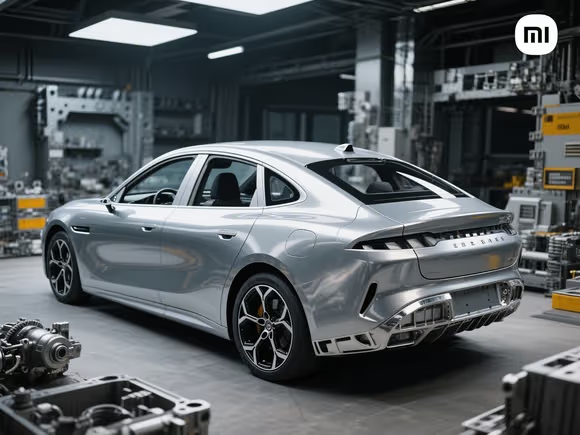