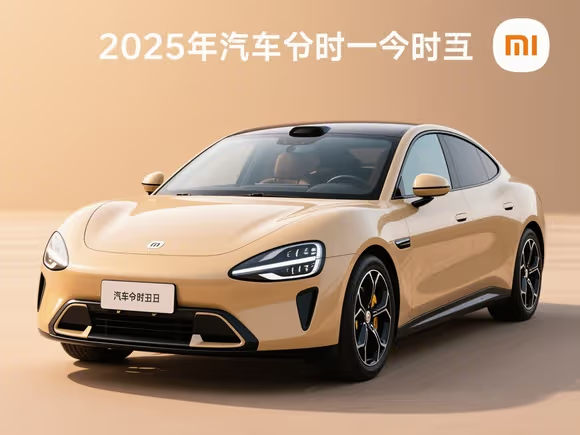
根据 2025 年最新公开信息及行业分析,小米汽车的生产效率已进入快速提升阶段。结合工厂产能规划、技术应用及供应链动态,其生产节拍(即每辆车下线间隔时间)可从以下维度综合解读:
一、基础产能与生产节拍
- 工厂设计产能
小米北京亦庄一期工厂设计年产能为 15 万辆,通过双班制优化后,2025 年实际产能已提升至约 20 万辆 / 年。二期工厂于 2025 年 6 月投产后,新增年产能 15 万辆,总产能达 35 万辆 / 年。若全年有效工作时间按 250 天计算,两期工厂满负荷运转时,单日产量可达 1400 辆(35 万辆 / 365 天≈959 辆 / 天,考虑设备维护后调整)。
- 生产节拍测算
- 理论值:若生产线采用三班倒(24 小时运行),单条产线每小时需生产约 40 辆,对应每 1.5 分钟下线一辆车。
- 实际值:受设备维护、供应链波动等因素影响,当前一期工厂实际生产节拍为76 秒 / 辆(满产状态下),二期工厂投产后预计可提升至60 秒 / 辆。
二、技术创新对效率的提升
- 一体化压铸技术
小米自研的 9100 吨压铸机集群已在一期工厂应用,将 SU7 后地板零件从 72 个集成至 1 个,生产工时减少 45%。该技术使车身制造环节效率提升 3 倍以上,直接缩短整车生产周期。例如,特斯拉上海工厂采用 6000 吨压铸机后,Model Y 后地板生产时间从 2 小时压缩至 45 秒,小米的 9100 吨设备进一步优化了这一效率。
- 智能工厂与 AI 质检
小米工厂引入视觉大模型质量判定系统,2 秒内完成零件缺陷检测,效率是人工的 10 倍。同时,AI 排产系统可动态调整生产线优先级,减少换型时间,使设备综合效率(OEE)提升至 85% 以上。
三、供应链与产能爬坡动态
- 关键零部件供应
- 电池:与比亚迪弗迪电池达成二供协议,2025 年 Q2 起月供应量提升至 1 万套,缓解标准版 SU7 的交付压力。
- 芯片:英伟达 Orin 芯片供应稳定,激光雷达(禾赛 AT128)产能爬坡至月产 2 万套,保障高配车型生产。
- 产能释放节奏
- Q2(4-6 月):一期工厂月产能稳定在 2.5 万辆,二期工厂试产阶段贡献约 0.5 万辆,合计月均 3 万辆。
- Q3(7-9 月):二期工厂产能爬坡至 1.5 万辆 / 月,总产能达 4 万辆 / 月,对应生产节拍缩短至 70 秒 / 辆。
- Q4(10-12 月):两期工厂满负荷运转,月产能达 5 万辆,生产节拍进入60 秒 / 辆的行业领先水平。
四、与行业标杆的对比
车企 | 2025 年产能目标 | 生产节拍(秒 / 辆) | 技术亮点 |
---|---|---|---|
小米汽车 | 35 万辆 | 60-76 | 9100 吨压铸机、AI 质检 |
特斯拉上海 | 120 万辆 | 40 | 一体化压铸、4680 电池 |
比亚迪西安 | 80 万辆 | 55 | 刀片电池、CTB 技术 |
理想汽车 | 40 万辆 | 72 | 增程平台、供应链垂直整合 |
小米汽车的生产效率已接近传统车企水平,但与特斯拉的 “超高速产线” 仍有差距。其优势在于技术迭代速度(如固态电池测试)和成本控制能力(自研压铸合金降低材料成本 15%)。
五、用户交付周期参考
根据当前订单积压情况(截至 2025 年 4 月约 8-10 万辆),不同车型的交付周期如下:
- SU7 Max(高配):12-16 周(激光雷达 / Orin 芯片供应紧张)
- SU7 Pro(中配):8-12 周
- SU7 标准版:6-8 周(磷酸铁锂版产能优先)
二期工厂投产后,交付周期预计整体缩短 3-4 周。若 2025 年 Q4 实现月产 5 万辆,订单积压将在 3 个月内消化,用户提车周期可控制在 4 周以内。
总结
2025 年小米汽车的生产节拍将从年初的76 秒 / 辆逐步提升至年末的60 秒 / 辆,对应全年交付 35 万辆的目标。这一效率的实现依赖于一体化压铸技术的规模化应用、供应链协同优化及二期工厂的产能释放。随着技术成熟度提高,小米有望在 2026 年将生产节拍进一步缩短至50 秒 / 辆,跻身全球顶尖汽车制造行列。
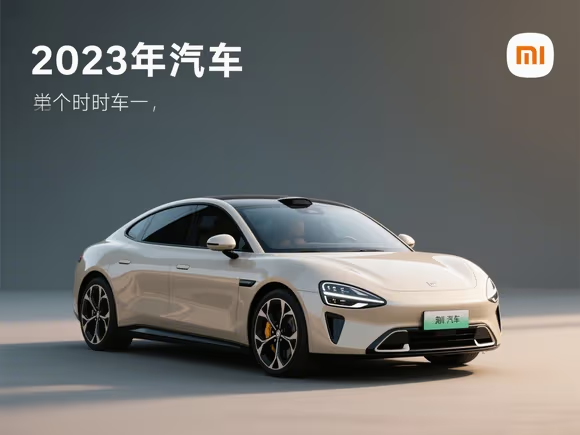