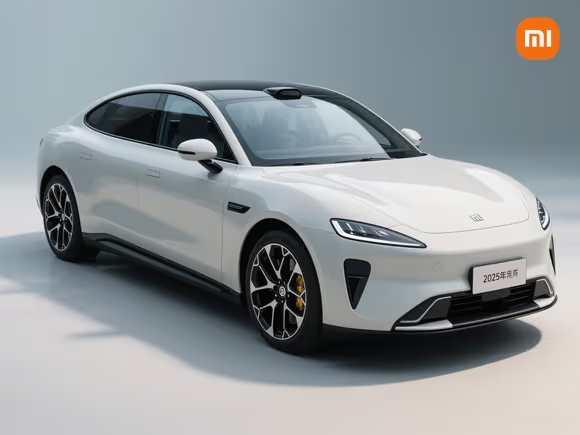
小米汽车在 2025 年的制造工艺展现出多维度的创新突破,其核心技术布局和生产体系已形成显著差异化竞争力。以下从六大核心领域解析其工艺亮点:
一、一体化压铸技术
小米超级工厂采用9100 吨泰坦合金压铸集群,将传统 72 个零件整合为单个大型压铸件,焊点减少 840 个,车身重量降低 17%,生产效率提升近一倍。通过340 倍标准大气压高压铸造 + 锻造复合工艺,金属分子结合密度提升 22%,整车扭转刚度达到 51000N・m/deg,接近百万级超跑水平。压铸后地板采用双层独立溃缩区设计,可按需更换受损部件,解决了传统大压铸维修成本高的行业痛点。
二、电池技术革命
- 麒麟 5.0 固态电池
与宁德时代联合研发的硫化物固态电池,能量密度达 500Wh/kg(传统液态电池约 250Wh/kg),支持 SU7 Pro + 车型 CLTC 续航 1200 公里。通过硫化物电解质 + 纳米陶瓷隔膜 + 铝塑复合封装三重防护,实现针刺、挤压无起火,热失控风险降低 90%。800V 高压平台配合自研热管理系统,12 分钟即可充电 80%,电池表面温度较液态电池低 22℃。 - CTB 倒置电芯技术
通过将电芯和泄压阀倒置,在热失控时引导能量向车底排放,乘员舱安全性提升 48%,同时释放 7mm 纵向空间,优化车内布局。
三、电机与电控创新
- V8s 超级电机:转速突破 27200 转 / 分钟(全球量产电机最高纪录),功率密度达 10.14kW/kg,驱动 SU7 Ultra 实现 2.78 秒零百加速,最高时速超 350km/h。
- 三电机四驱系统:前轴 1 台 V6 电机 + 后轴双 V8s 电机,综合马力超 1500 匹,15.07 秒完成 0-300km/h 加速,动力性能对标顶级超跑。
- 电控系统:申请 242 项专利,BMS 4.0 系统实现电芯级压力 / 温度实时监控,热失控前 15 分钟预警,能量回收效率提升至 32%。
四、智能驾驶与生态融合
- X-Pilot 4.0 系统:搭载 31 个高精度传感器(4 颗 128 线激光雷达 + 8 颗 800 万像素摄像头),配合 NVIDIA Orin-X 芯片组实现 1024TOPS 算力,城市 NOA 功能覆盖全国 45 个主要城市,可完成无保护路口掉头、隧道自动跟车等复杂场景。
- 智能座舱:一体化超清三联屏 + AR-HUD 增强现实导航,车机系统与小米手机、智能家居深度打通,支持语音远程控制 2000 + 米家设备。
五、绿色制造体系
- 光伏电站:工厂屋顶铺设 16.2MW 分布式光伏面板,年发电量 1640 万千瓦时,减少二氧化碳排放 9905 吨,相当于种植 54 万棵树。
- 循环材料:泰坦合金压铸件采用 30% 再生铝,单个零件碳减排 352.53kg;电池包支持梯次利用,寿命结束后材料回收率超 95%。
- 环保工艺:涂装车间采用水性涂料,VOCs 排放较传统工艺降低 70%;废水处理系统实现 95% 循环利用,优于首都排放标准。
六、生产基地与产能布局
- 北京亦庄工厂:一期年产能 30 万辆,每 76 秒下线一辆新车,二期工厂 2025 年 6 月投产,整体产能提升至 35 万辆 / 年。
- 武汉基地:规划占地 2000 亩,采用 “黑灯工厂” 设计,自动化率达 95%,辐射华中市场。
- 全球供应链:与宁德时代、汇川技术等 46 家 A 股上市公司深度合作,核心零部件本地化采购率超 85%,通过 “南北双基地” 分散供应链风险。
总结
小米汽车 2025 年的工艺突破,本质是科技生态与制造工业的深度融合。通过一体化压铸、固态电池、超级电机等硬核技术,以及智能制造、绿色生产体系的构建,小米不仅实现了产品性能的跃升,更通过生态协同(如米家设备互联)和成本控制(供应链整合),重新定义了智能电动车的价值标准。这种 “技术普惠” 策略,正在加速其从科技公司向汽车制造巨头的转型。
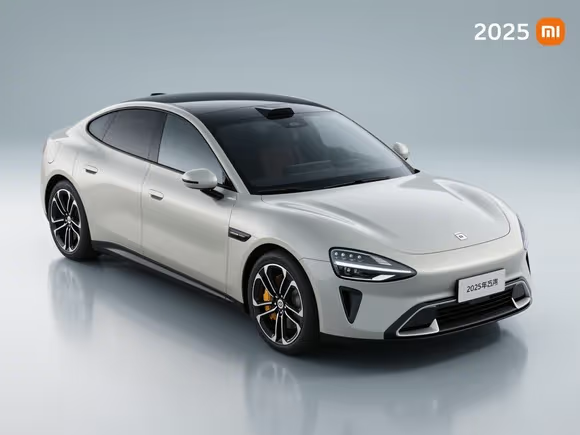