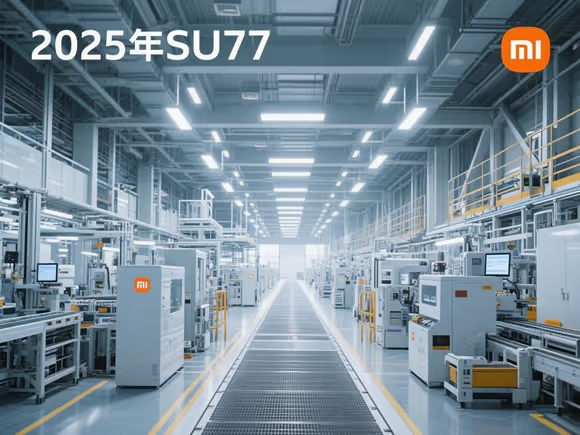
截至 2025 年 4 月,小米 SU7 的生产主要依托北京亦庄的自建工厂,该工厂以高度自动化和智能化为核心竞争力,但尚未实现完全意义上的 “无人工厂”。以下是基于公开信息的综合分析:
一、小米 SU7 工厂的自动化与智能化水平
- 生产工艺的高度自动化
小米汽车工厂采用了 “黑灯工厂” 的设计理念,关键工艺如冲压、焊接、涂装、总装等环节实现 100% 自动化。工厂配备超过 700 台工业机器人,包括 9100 吨一体化压铸机、六轴全自动拧紧机械臂等,每 76 秒即可下线一台小米 SU7。例如,电池模组的装配采用 “机器人 + 3D 点云视觉 + 力控感知” 技术,精度达 0.2mm,确保零损伤装配。
- AI 与数字化的深度融合
- 质量检测:AI 视觉系统以 0.1 秒的速度完成零部件表面缺陷检测,结合工业大数据实现全流程追溯。
- 物流管理:AMR 自主导航机器人替代传统 AGV,可动态避让行人,优化物料配送效率。
- 生产调度:基于数字孪生技术的虚拟工厂实时模拟生产流程,支持柔性化排产。
- 绿色制造与可持续性
工厂顶部覆盖光伏板,年发电量达 1640 万度,废水废气处理效率超 99%,废重金属实现零排放。这种设计不仅降低碳排放,还通过能源自给提升了供应链韧性。
二、小米 SU7 工厂的人力配置与行业对比
- 人机协作的生产模式
尽管自动化率高达 91%,工厂仍需约 2000 名员工,其中 50% 为研发人员,负责算法优化、设备调试等非重复性工作。例如,焊接工转型为机械臂操作员,质检员学习 AI 系统维护,体现了 “技术倒逼技能升级” 的趋势。
- 与行业标杆的差距
特斯拉上海超级工厂的自动化率超过 95%,且已实现部分工序的无人化(如电池包组装)。相比之下,小米工厂在复杂装配环节(如内饰安装、线束排布)仍依赖人机协作,尚未突破 “最后一公里” 的自动化瓶颈。
三、小米 SU7 工厂的技术突破与挑战
- 核心技术亮点
- 大压铸工艺:采用 9100 吨压铸机实现车身一体化成型,减少零部件数量,提升车身强度。
- 电池安全设计:电芯倒置布局避免电解液喷溅,配合 “车 - 云” 健康监测系统,实现碰撞后 5 秒内主动放电。
- 智能驾驶验证:工厂内建有 2.5 公里测试跑道,涵盖 18 种路况,支持 Xiaomi Pilot 系统的全场景测试。
- 面临的挑战
- 产能爬坡压力:截至 2025 年 4 月,小米 SU7 累计订单超 32 万辆,但交付量仅 18 万辆,产能瓶颈凸显。二期工厂预计 2025 年 6 月投产,可能缓解压力。
- 技术迭代风险:YU7 车型因英伟达 Thor 芯片流片延迟被迫推迟,暴露了对外部技术的依赖。
- 安全信任重建:SU7 连续发生碰撞起火事故,尽管官方归因于外部因素,但仍需通过技术升级(如更严格的电池防护)重塑市场信心。
四、未来展望:无人工厂的可能性
- 技术演进路径
小米已布局人形机器人(如 CyberOne)和具身智能,未来可能将其应用于工厂的复杂操作环节。例如,协作机器人可逐步替代人工完成内饰装配、故障检修等任务。
- 行业趋势参考
上汽通用武汉奥特能超级工厂等案例显示,2025 年汽车制造业更倾向于 “高度自动化 + 局部无人化”,而非全面无人工厂。小米若想实现突破,需在 AI 决策、柔性制造等领域加大投入。
五、总结
小米 SU7 工厂代表了中国新能源汽车制造的先进水平,其高度自动化、AI 赋能和绿色生产模式已接近 “无人工厂” 的雏形。然而,受制于技术成熟度、成本效益和行业标准,完全无人化生产在 2025 年仍处于探索阶段。未来,随着人形机器人、大模型等技术的渗透,小米有望在 3-5 年内实现关键工序的无人化突破,进一步巩固其在智能制造领域的竞争力。
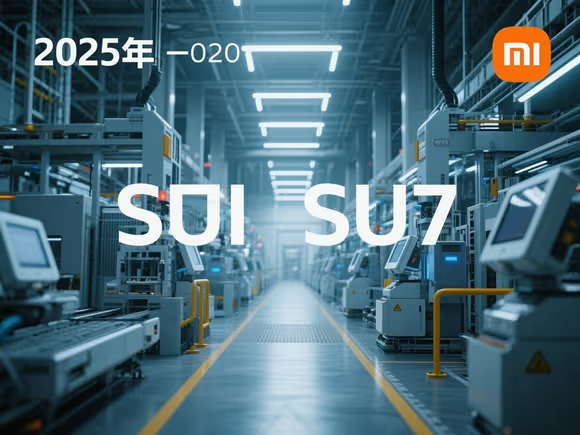