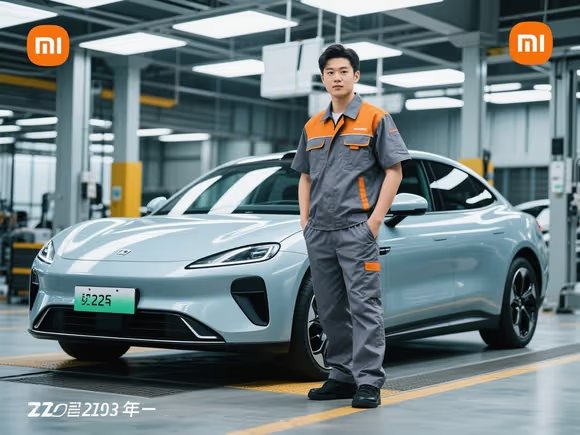
小米汽车在 2025 年的工装体系已进入全面量产验证与产能爬坡的关键阶段,其技术布局和生产规划展现出对智能制造的深度整合。以下从核心技术突破、产能建设、供应链协同及未来趋势四个维度展开分析:
一、核心工装技术突破:重构汽车制造范式
1. 9100 吨一体化压铸集群
小米自研的超级压铸技术已实现规模化应用,其核心设备为 9100 吨锁模力的巨型压铸机,配套 60 余台设备组成的压铸岛集群,占地达 840 平方米。通过该技术,小米 SU7 的后地板实现 72 个零件一体化成型,焊点减少 840 个,生产工时缩短 45%,同时整车扭转刚度提升至 51000N・m/deg,达到传统油车的两倍。材料端采用自研的 “小米泰坦合金”,通过 AI 仿真系统从 1016 万种配方中筛选出最优方案,支持 30% 循环铝使用,单零件碳减排 352.53kg,年产能相当于种植 488 万棵树。
2. 智能装配线革新
2025 年 4 月获批的 “分装线工装和装配线” 专利(CN222725993U),通过基架翻转设计实现热管理总成的多工位协同装配,将传统 3 个工位的操作压缩至 1 个,配合温度补偿算法和视觉大模型检测系统,装配精度达 0.1 毫米级,检测效率提升 10 倍。该技术已在二期工厂部署,预计使总装线效率提升 30% 以上。
3. 电池车身一体化(CTC)技术
小米最新专利 “电池及车身一体化构造与车辆”(CN222725993U)将电池包与门槛梁深度融合,通过横梁结构增强抗侧碰能力,同时减少额外部件重量,为续航提升和空间优化提供可能。该技术预计 2025 年下半年在 MX11 车型(小米 SUV)上试点应用。
二、产能建设:从工厂到生态的扩张
1. 二期工厂量产在即
位于北京通州马驹桥的二期工厂于 2025 年 4 月 16 日完成规划验收,总建筑面积 40 万平方米,设计年产能 30 万辆,预计 7 月投产。该工厂采用 “冲压 - 压铸 - 焊装 - 涂装 - 总装” 全工艺布局,其中压铸车间配备 4 台 9100 吨压铸机集群,可实现每分钟 1 件的生产节拍。
2. 三期工厂规划启动
紧邻二期工厂的 52 公顷地块已被纳入工业用地规划,未来将建设三期工厂,重点布局高压电驱、智能座舱等核心零部件生产线。结合一期工厂 15 万辆产能,2025 年小米汽车总产能将突破 50 万辆,支撑全年 35 万辆交付目标。
3. 供应链本地化率提升
小米已构建覆盖模具(超达装备)、车身(联明股份)、热管理(津荣天宇)、电子(大富科技)的供应链体系,本地化率达 85%。其中,宁波赛维达参与全球首个一体化压铸项目研发,提供高精度模具;力劲集团定制的 9100 吨压铸机实现国产化替代,成本较进口设备降低 40%。
三、供应链协同:效率与质量的双重保障
1. 模块化生产模式
采用 “压铸岛 + 柔性焊装线” 的模块化布局,后地板压铸与电池包装配同步进行,实现 “2 小时下线一台车” 的节拍。通过自研的 “小米智造云平台”,实时监控 433 项工艺参数,异常响应时间缩短至 2 秒。
2. 质量控制体系
视觉大模型检测系统可识别 0.01 毫米级缺陷,配合超声波探伤和 X 射线成像,实现关键焊点 100% 检测。2024 年量产车型 SU7 的 PPH(百车故障数)已降至 85,达到行业头部水平。
3. 成本控制策略
通过一体化压铸减少零件数量,SU7 后地板生产成本较传统工艺降低 28%。同时,二期工厂采用光伏 + 储能系统,单位产能能耗较一期下降 15%,年节约电费超 2000 万元。
四、未来趋势:从制造到智造的跃迁
1. 低空经济布局
小米已与航天科工合作研发车载级轻量化材料,计划 2026 年将一体化压铸技术应用于低空飞行器结构件,探索 “车 - 空” 制造协同。
2. AI 驱动的工装升级
正在开发的 “数字孪生工厂” 系统,可通过虚拟仿真优化工装夹具设计,将新车型开发周期从 24 个月压缩至 18 个月。预计 2025 年底实现压铸工艺参数的 AI 自主优化。
3. 可持续制造实践
除循环铝应用外,小米计划 2025 年在武汉工厂试点 “零碳压铸岛”,采用绿电和碳捕捉技术,目标单台压铸机年减碳量达 3000 吨。
总结
2025 年的小米汽车工装体系,已从单纯的设备部署升级为 “技术 - 产能 - 生态” 三位一体的智能制造平台。其核心突破在于通过自研大压铸技术重构生产流程,结合模块化布局和 AI 质检实现效率与质量的双提升。随着二期工厂投产和三期规划落地,小米正加速构建 “超级工厂矩阵”,为其在新能源汽车赛道的长期竞争奠定基础。未来,随着低空经济和零碳技术的融入,小米有望进一步拓展工装技术的应用边界,引领汽车制造的下一个变革周期。
