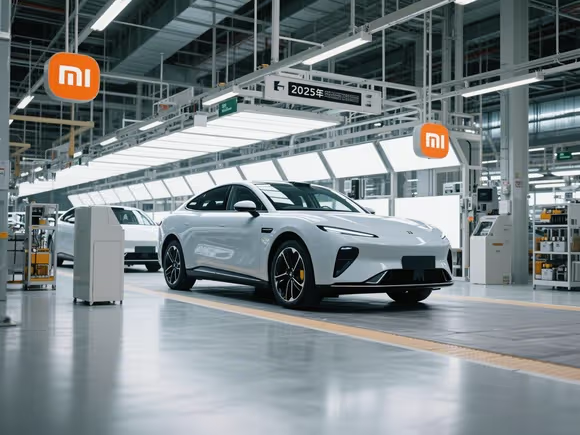
截至 2025 年,小米汽车车间已成为全球智能制造的标杆,其北京亦庄超级工厂和规划中的武汉基地共同构建起覆盖华北与华中的产能网络。以下从生产布局、技术创新、产能释放、供应链协同及可持续发展五个维度展开分析:
一、生产布局:双工厂协同,覆盖全国市场
- 北京亦庄超级工厂
- 一期工厂:自 2024 年 4 月投产以来,已实现单月交付超 2.9 万辆。工厂设有压铸、冲压、车身、涂装、总装、电池六大车间,配备 700 余台机器人,关键工艺 100% 自动化。通过双班生产模式,实际产能已突破一期设计的 15 万辆 / 年,2024 年全年交付 13.68 万辆。
- 二期工厂:紧邻一期建设,占地面积扩展至 105 公顷,2025 年 6 月竣工后产能将提升至 30 万辆 / 年。二期引入更柔性的生产线,可同时支持 SU7、YU7 等多车型混流生产,并新增 AI 质检系统和数字孪生技术,实现生产数据实时反馈优化。
- 武汉工厂规划
- 尽管官方尚未正式宣布,但武汉经开区已启动相关地块平整,计划建设第三座汽车工厂。该工厂可能与东风集团合作,利用现有产能快速投产,预计 2025 年底公布细节。武汉基地将辐射中部及西南市场,与北京工厂形成互补。
二、技术创新:全栈自研重构制造体系
- 超级大压铸技术
- 小米自研 9100 吨锁模力压铸机集群,配合泰坦合金材料,实现 72 合 1 一体化压铸后地板,焊接点减少 840 处,车身减重 10%。该技术已应用于 SU7 生产,二期工厂将进一步扩展至前舱等更多部件。
- 智能质检与预测性维护
- X-Eye 智能质检系统:通过 AI 分析 X 光片,实现焊点、焊缝的微米级检测,缺陷识别准确率达 99.98%。
- 预测性维护:基于工业大数据算法,提前 500 个测试循环预测装备寿命,减少停机损失 10%。
- 数字孪生与柔性生产
- 工厂采用数字孪生技术模拟产线运行,支持快速切换车型配置。例如,SU7 Ultra 的定制化订单可通过虚拟调试实现 24 小时内工艺参数优化。
三、产能释放:35 万辆目标下的挑战与应对
- 交付目标提升
- 2025 年交付目标从 30 万辆上调至 35 万辆,第一季度已交付 7.56 万辆,完成率 21.61%。SU7 Ultra 上市 3 天锁单超 1 万辆,YU7 预计 6 月量产,产能压力显著。
- 产能爬坡策略
- 北京工厂:通过优化产线流程,单班产能从 7000 辆 / 月提升至 1.2 万辆,双班模式下实际产能接近设计值的 200%。
- 供应链协同:与宁德时代、比亚迪共建电芯工厂,确保电池供应;博世、汇川技术等核心供应商在工厂周边设立卫星仓,实现零部件 2 小时响应。
四、供应链协同:深度绑定与垂直整合
- 核心供应商
- 电池:比亚迪刀片电池(SU7 标准版)与宁德时代三元锂电池(SU7 Ultra)双线并行,武汉电芯工厂投产后将实现部分自产。
- 电驱:汇川联合动力提供永磁同步电机,联合电子供应碳化硅电控模块,系统效率达 97.5%。
- 智能驾驶:禾赛科技激光雷达、黑芝麻智能 A2000 芯片等构成感知与计算平台,支持城市 NOA 功能。
- 本地化采购
- 北京工厂周边 30 公里内聚集了 1200 家零部件企业,包括海斯坦普、麦格纳等,本地化率超 70%。二期工厂将引入更多长沙、武汉等地供应商,如蓝思科技的智能座舱屏幕。
五、可持续发展:绿色制造与循环经济
- 能源结构
- 车间顶部铺设光伏板,年发电量 1640 万度,满足 15% 的用电需求;厂房屋顶雨水回收系统每年节水 3 万吨。
- 工艺优化
- 涂装车间采用水性涂料和 3C1B 工艺,VOC 排放降低 60%;废重金属 100% 回收,电池梯次利用项目已落地。
- 材料创新
- 泰坦合金材料碳排放较传统铝合金降低 30%;内饰件采用海洋回收塑料,单车使用量超 50 公斤。
未来展望:从制造到智造的跨越
2025 年,小米汽车车间将进一步深化 “软件定义制造” 理念:
- AI 大模型应用:在工艺参数调优、供应链排程等环节部署生成式 AI,预计提升生产效率 15%。
- 武汉工厂落地:若武汉基地启动,将采用 “黑灯工厂” 模式,实现全流程无人化生产。
- 全球化布局:计划在东南亚、欧洲设立 KD 工厂,输出中国智造经验。
小米正以 “76 秒下线一台车” 的速度,重新定义汽车工业的效率与创新边界。
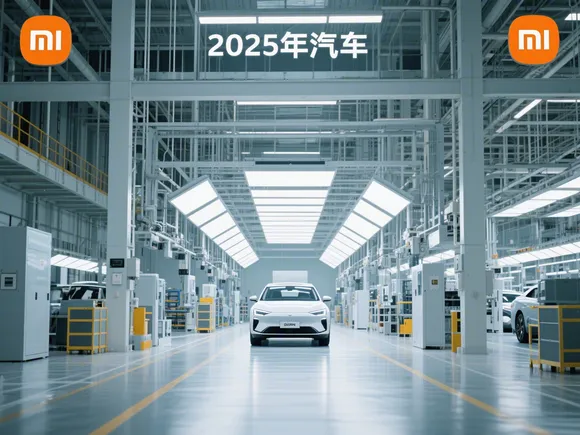